Stainless steel is undoubtedly one of the most commonly used materials worldwide. It’s vital in the construction of buildings, automobiles, bridges, kitchenware, and many more. You may be wondering, what exactly is stainless steel, and how is it made? In this blog post, we will give you an overview of the fascinating process of creating this durable and versatile material. Stainless steel is a material that is used in a variety of products, including flanges, bars, plates, sheets, and rods. This versatile material is valued for its durability and resistance to corrosion, making it a popular choice for applications where strength and longevity are critical.
It all starts with iron ore, which is mined from the ground and transported to the steel mill. Steelmakers melt the iron ore, along with a proportionate amount of coal and limestone, in a furnace. This procedure turns the iron ore into molten iron. When the impurities are removed, they are left with liquid pig iron. The pig iron is then blended with scrap metal and other alloys to create the final raw material.
Melting the Raw Materials
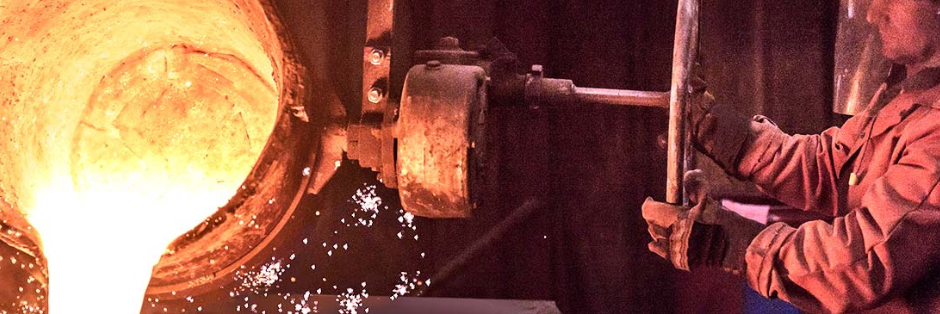
Melting the raw materials is an essential process in many manufacturing industries. It involves heating solid raw materials to a temperature that causes them to become liquid. This enables manufacturers to reshape, mold, or cast the materials into the desired shape or form. The process of melting can be challenging, depending on the type of raw material, as some materials have high melting points that require substantial energy to heat them to the right temperature. Nonetheless, this process is crucial in producing various products, from metals, glass, and plastics to concrete and ceramics. It is an important step in the manufacturing process that ensures the final product meets the desired quality and standards.
The next step is to make the steel out of the pig iron. The steelmaker will perform various refining techniques to remove carbon and other impurities from the pig iron. One of the most common refining methods is the basic oxygen process, which involves injecting oxygen into the molten pig iron. Argon and nitrogen gas are also added to the mixture to purify the steel further. That produces a high-quality steel called carbon steel, which is low in carbon content and used in construction.
Heat treatment and annealing For metals
Heat treatment and annealing are processes employed in the world of metallurgy to improve the mechanical and physical properties of metals. Annealing is a slower process that requires heating the metal to specific temperatures, depending on the metal’s composition, and allowing it to cool slowly. This process allows the molecules to align themselves in a less stressful pattern, making the metal more ductile and pliable. Heat treatment, on the other hand, is a quicker process that involves heating the metal and then quenching it with water or oil. This forces the molecules to arrange themselves in a more uniform and rigid structure, resulting in greater hardness and strength. Both processes are crucial in shaping and strengthening a wide range of metals to meet various industrial needs, and they are essential in the manufacturing of everything from kitchen utensils to airplanes.
However, the process of producing stainless steel requires an additional step. Manufacturers must blend other components with the steel, including chromium and nickel, up to about 10% and 30%, respectively. The nickel helps to strengthen the material and improve its corrosion resistance, while chromium gives it that attractive shiny appearance.
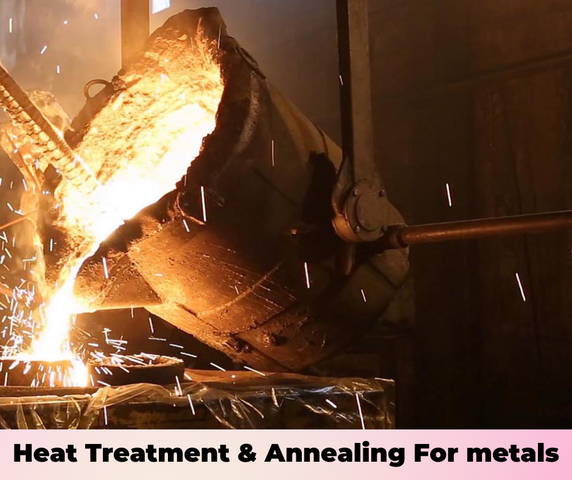
Once the chromium and nickel are added, the steel needs to be melted again to blend the ingredients evenly. The furnace the steelmakers use is much different from the one used in the initial process. For stainless steel, an electric arc furnace, induction furnace, or vacuum furnace is typically used, depending on the manufacturer's preference. The components are melted at temperatures exceeding 1700 degrees Celsius, which turns the steel into a liquid form.
The molten steel is then put into molds and left to cool. The cooling period is essential, as rapid cooling causes deformations in the material. Slow cooling, on the other hand, makes sure that the material aligns itself correctly, creating a strong and durable product.
Forming the Metal
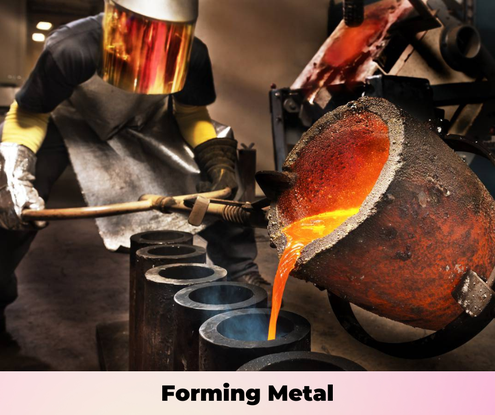
Forming metal can be a truly fascinating process. The malleability of metal allows it to be shaped into an endless variety of forms, from the simplest to the most intricate. The process begins with raw metal, which is heated to make it easier to work with. With skill and precision, the metal is pounded and shaped using hammers and anvils, or molded with presses and dies. Each step requires careful attention to detail, as even the slightest miscalculation can result in a flawed product. However, the end result is almost always stunning – a beautiful, functional work of art that showcases the versatility and beauty of metal. Whether it be a decorative piece or an essential component of a larger project, the skillful formation of metal is an impressive feat that requires a high degree of expertise and dedication.
Cutting and shaping Material
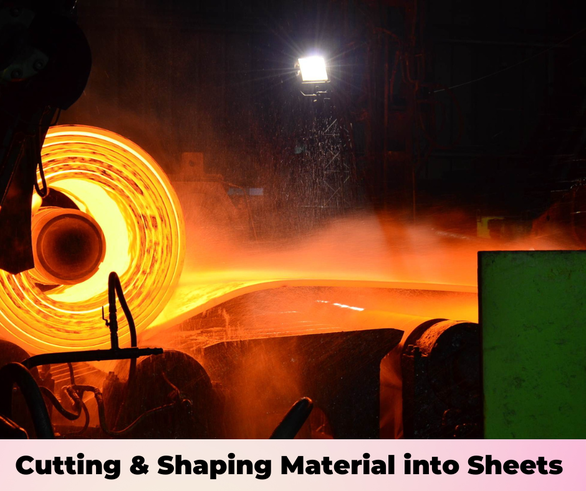
Cutting and shaping of material is an essential aspect of every manufacturing process. Whether you're dealing with wood, metal, or plastic, cutting and shaping material with precision is critical to creating high-quality products. It's not just about removing excess material; it's about crafting the material to create something unique and functional. From furniture to electronics, everything we use in our daily lives has been cut and shaped by someone. This process requires the right tools, great attention to detail, and experience to bring out the right attributes in the material. The precision of the final cut can determine just how successful a product will be. When done correctly, cutting and shaping material can produce beautiful pieces that stand the test of time.
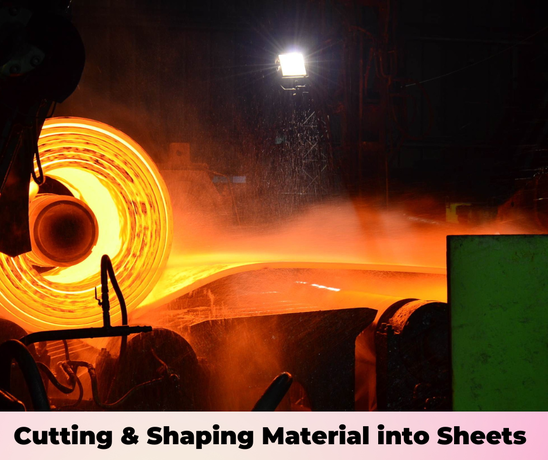
Conclusion:
The process of producing stainless steel may seem complicated, but it involves several simple steps that give the material its unique properties. From mining iron ore to melting, refining, and adding chromium and nickel, the end product is a durable material that can withstand the test of time. With its attractive shiny appearance and resistance to corrosion, stainless steel is an essential material found in many applications, ranging from home appliances to industrial machinery.
Add comment
Comments